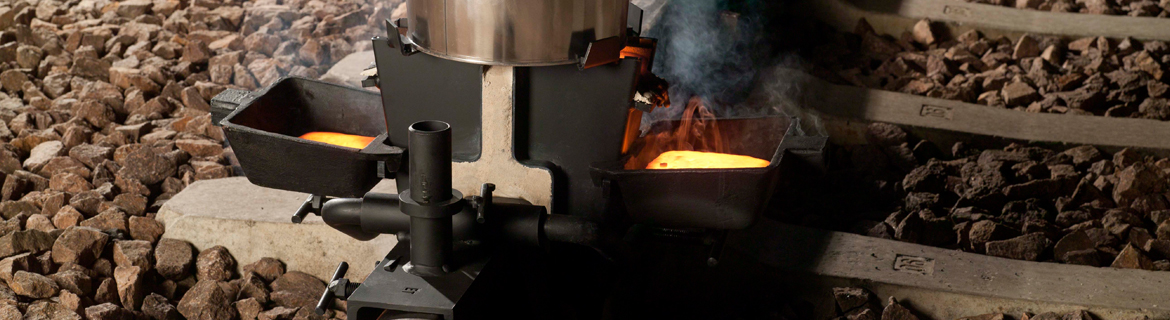
THERMIT® welding processes
Using the Thermit® welding process, virtually all rails of widely varying profiles and grades can be joined together without gaps. Thermit® is composed of aluminium granules and iron oxide, which has a strong exothermal reaction after initial ignition. The high heat of the reaction makes it possible to produce liquid steel at up to 2,300°C without using external sources of energy, as a result of which the ends of rails can be welded together. We can therefore guarantee the secured connection of the rails in heavy-load and high-speed networks, while at the same time increasing travelling comfort and the lifetime of the track.
We offer the following processes:
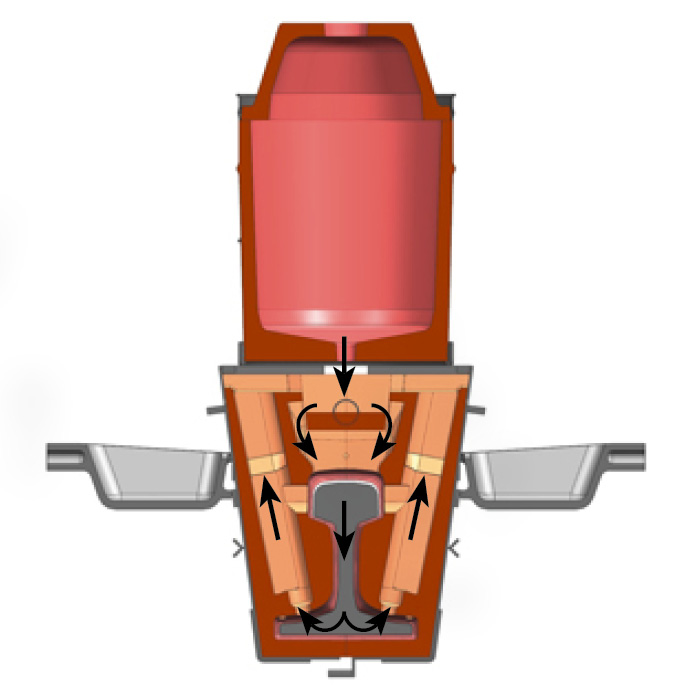
THERMIT® SKV-ELITE L25
Fast and safe welding of flat-bottom rails
With Thermit® SkV-Elite L25 you benefit from a dependable product suitable for construction sites for the welding of rail. The process is reliable, robust, and ideally suited for connecting flat-bottom rails in all types of operating track systems, for all speeds, in heavy haul traffic and also during high-density traffic due to the short execution time.
Downloads
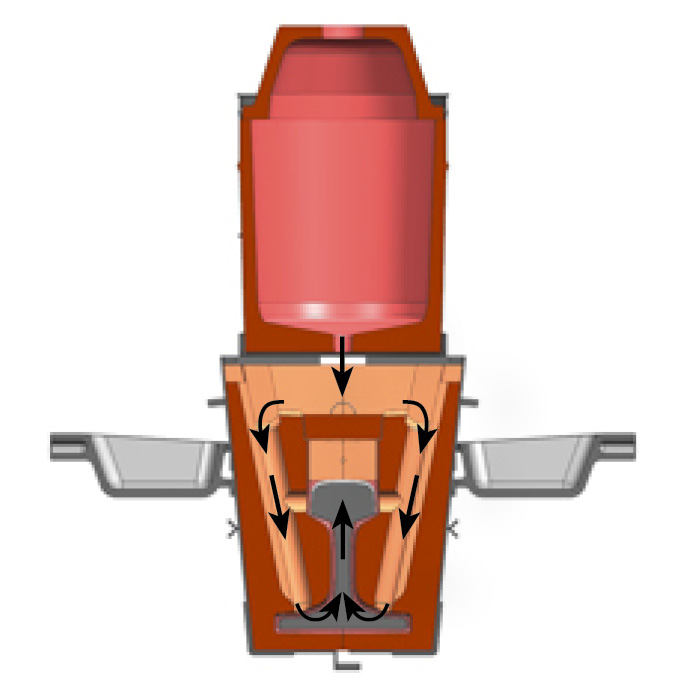
THERMIT® SOW-5
Universal welding process for flat-bottom rails
Thermit® SoW-5 is one of the best technologies for creating continuously welded track. This process means effortless use on construction sites and therefore ensures excellent availability of routes. Thermit® SoW-5 is ideally suited for high strength rail grades but produces Thermit® welds on operating track systems of all speeds in heavy haul traffic and also in high-density traffic.
Downloads
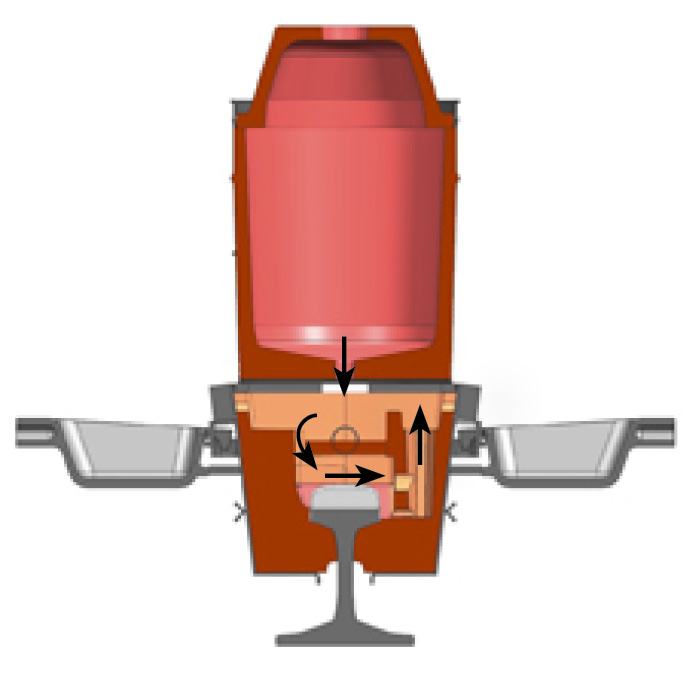
THERMIT® HEAD REPAIR
Original Thermit® repair weld for flat-bottom rails
Thermit® Head Repair is ideal for rectifying faults on the running surface of flat-bottom rails of various profiles. Depending on the severity of the defect, it may be necessary to remove the relevant sections and install replacement rails. However, squats, indentations, spalling and wheel burns can be repaired with our repair weld process.
Downloads
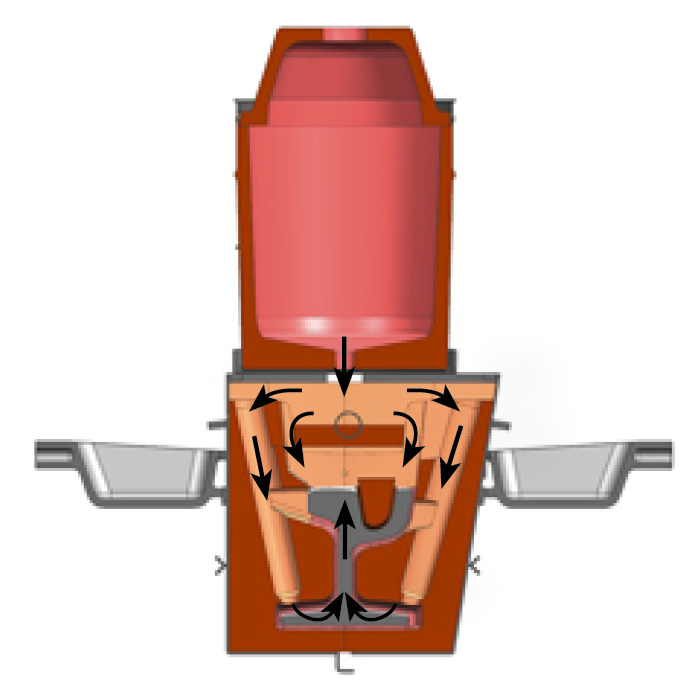
THERMIT® SRZ
Fast and safe welding of grooved rails
Grooved rails can be connected safely and reliably using the Thermit® process. There is no process that is faster than the Thermit® SRZ welding process. It is ideal for geometrically complex connections combined with grooved rails of all steel types. Thermit® SRZ is largely user-independent and therefore safer when used in rail compared to electric arc welding.
Downloads
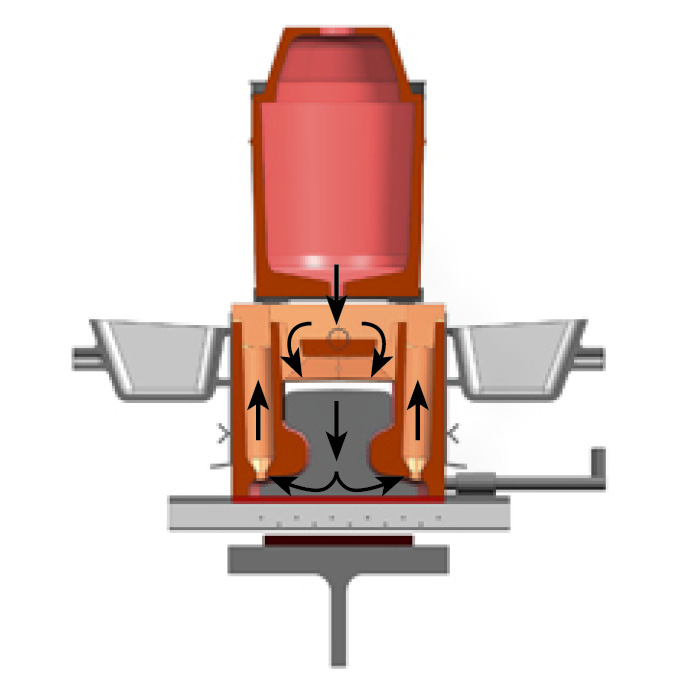
THERMIT® SRZ
Best technology for high quality
Welding crane rails requires a high degree of precision, efficiency and safety. Our Thermit® SKS welding process means you have the best technology available for satisfying the stringent demands of crane rail welds with excellent welding performance. This process is the alternative to arc joint welding as its use is largely user-independent.
Downloads
Service
Are you interested in our range of products and services or have questions? Please contact us. We will be glad to help you.